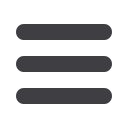
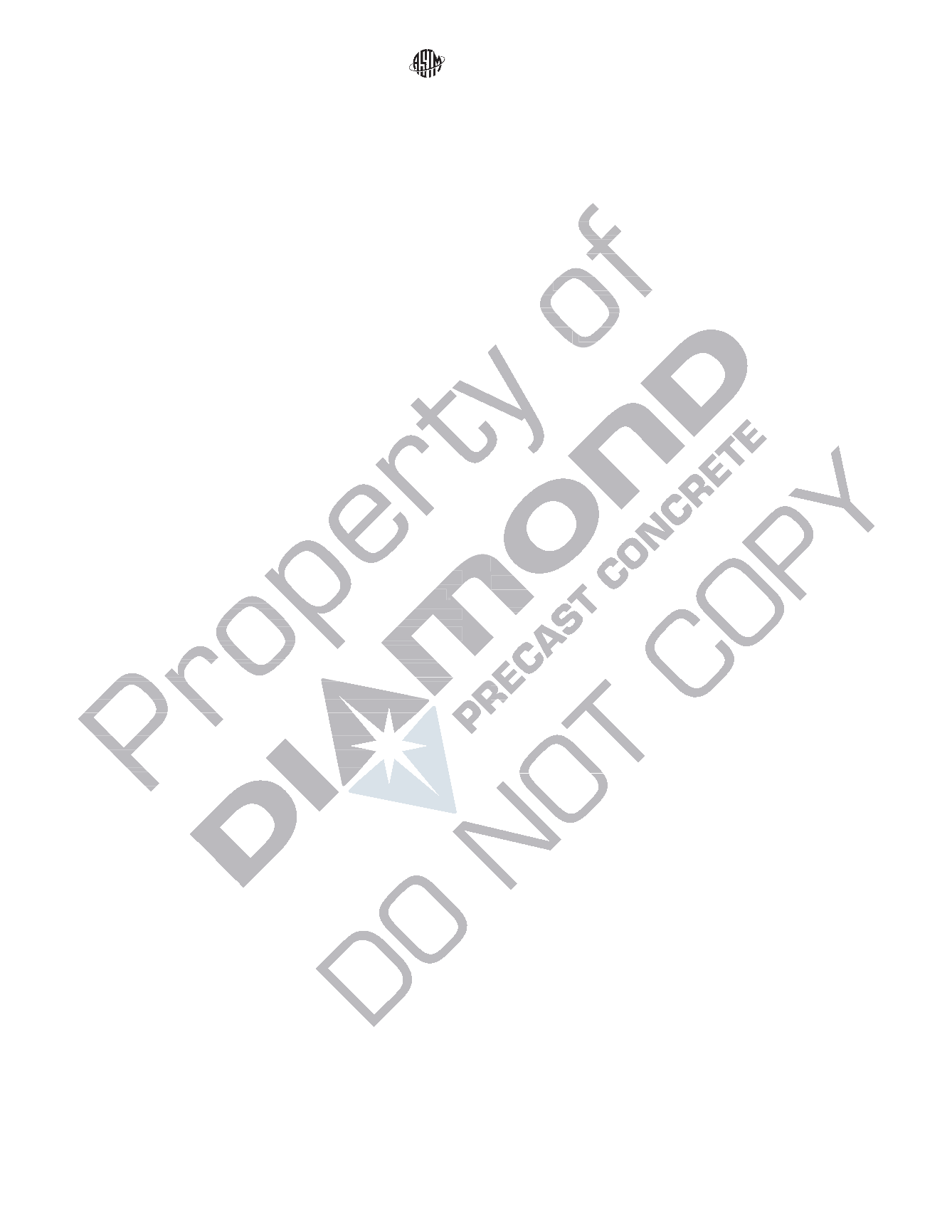
15.4.1
Base Section Circumferential Reinforcement—
Circumferential reinforcement shall meet all the requirements
of Section
14
, except that Paragraph 14.5 is not permitted.
15.4.2
Base Slab Reinforcement:
15.4.2.1 A layer of reinforcement shall be placed above the
midpoint, and shall have a minimum area of 250 mm
2
/linear m
in both directions.
15.4.2.2 The minimum protective cover over the reinforce-
ment shall be 25 mm.
15.4.3
Longitudinal Members—
Longitudinal bars or mem-
bers used to maintain a cage of circumferential reinforcement
in shape and position within the form shall meet all the
requirements of Section
14
.
15.4.4
Joint Reinforcement—
The mating surface of the base
section joint is not required to contain circumferential rein-
forcement.
N
OTE
4—(Advisory) Base sections with multiple openings, large
openings, or both may require special consideration of their handling
reinforcement.
15.5
Physical Requirements—
Physical requirements for test
shall conform to the requirements of Section 8.
15.5.1
Proof-of-Design Test:
15.5.1.1 If
15.2.2.1
has been designated as the basis of
acceptance, one base section or base slab for each design shall
be tested unless the owner has indicated otherwise.
15.5.1.2 The base section or base slab proof-of-design test
procedures shall be in accordance with Test Methods
C497
.
15.5.1.3 The ultimate test load shall be the sum of at least
130 % of the dead load on the base section or base slab plus at
least 217 % of the live load on the slab. Dead load is the weight
of the column of earth cover plus the weight of the riser
section(s) plus surcharge transmitted through the riser sec-
tion(s) to the base section or base slab. Live load is the
maximum anticipated wheel load that may be transmitted
through the riser to the base section or base slab. The ultimate
test load shall be applied to the base section or base slab as a
uniformly distributed load.
15.5.1.4 The base section or base slab shall be acceptable if
it supports the required ultimate test load without failure.
Ultimate strength failure is defined as the inability of the slab
to resist an increase in the applied load.
15.5.1.5 When agreed upon by the owner and manufacturer,
the base section or base slab shall be acceptable based on
certified copies of the results of tests performed on identical
base sections or base slabs instead of requiring new proof-of-
design acceptance test.
15.6
Joints—
Precast reinforced base sections shall be de-
signed and manufactured with a male or female ends, so that
the assembled manhole base, riser and top will make a
continuous and uniform manhole, compatible with the toler-
ances given in
15.7
.
15.6.1 Joints are designed to perform in axial compression;
therefore, shear or load testing of the joint is not required.
15.7
Permissible Variations:
15.7.1
Internal Diameter—
The internal diameter of base
sections shall not vary more than 1 %.
15.7.2
Thickness—
The thickness of a base slabs with or
without benching shall be not less than that prescribed in the
design by more than 5 %. A thickness greater than that
prescribed in the design shall not be cause for rejection.
15.7.3
Height of Two Opposite Sides—
Variations in laying
heights of two opposite sides of base sections shall be not more
than 16 mm.
15.7.4
Height of Sections—
The underrun in height of a base
section shall be not more than 20 mm/m of height with a
maximum of 13 mm in any one base section.
15.7.5
Position of Reinforcement—
For base slabs with
monolithic benched inverts with a 100 mm thickness, the
maximum variation in the position of reinforcement from that
prescribed in
15.4
shall be
6
10 % of the thickness or
6
6 mm,
whichever is greater. For base slabs with a thickness greater
than 100-mm, the maximum variation shall be
6
10 % of the
thickness or
6
16 mm, whichever is the lesser. In no case,
however, shall the cover over the reinforcement be less than 19
mm. The preceding minimum cover limitation does not apply
to the mating surfaces of base section joints.
15.7.6
Area of Reinforcement—
Steel reinforcement areas
that are 10 mm
2
/linear m less than called for by design shall be
considered as meeting the required steel reinforcement area.
15.8
Rejection:
15.8.1 Base sections shall be subject to rejection for failure
to conform to any of the specification requirements. In
addition, an individual base section shall be subject to rejection
because of any of the following:
15.8.1.1 Fractures or cracks passing through the riser wall,
except or a single end crack that does not exceed the depth of
the joint.
15.8.1.2 Defects that indicate mixing and molding not in
compliance with
7.1
or surface defects indicating honey-
combed or open texture that would adversely affect the
function of the base section.
15.8.1.3 The planes of the ends are not perpendicular to the
longitudinal axis of the base section, within the limits of
permissible variations prescribed in
15.7
.
15.8.1.4 Damaged or cracked ends, where such damage
would prevent making a satisfactory joint.
15.8.1.5 Any continuous crack having a surface width of 0.3
mm, or more and extending for a length of 300 mm or more,
regardless of position in the base section.
16. Steps and Ladders
16.1
Scope:
16.1.1 This section covers manhole steps and ladders used
for providing access through manholes for use in sewer and
water works.
16.1.2 The user of this specification is advised that access
through manholes may be by steps that are cast, mortared, or
attached by mechanical means into the walls of base, riser, or
conical top sections or by ladder.
16.2
Acceptance—
Unless otherwise designated by the
owner at the time of, or before, placing an order, acceptance of
steps and ladders installed in manholes will be on the basis of
tests and inspection of the completed product.
C478M − 15
8
Copyright by ASTM Int'l (all rights reserved); Mon Jun 29 17:17:40 EDT 2015
Downloaded/printed by
Jed Friesen (Predl Systems) pursuant to License Agreement. No further reproductions authorized.