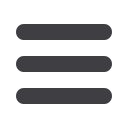
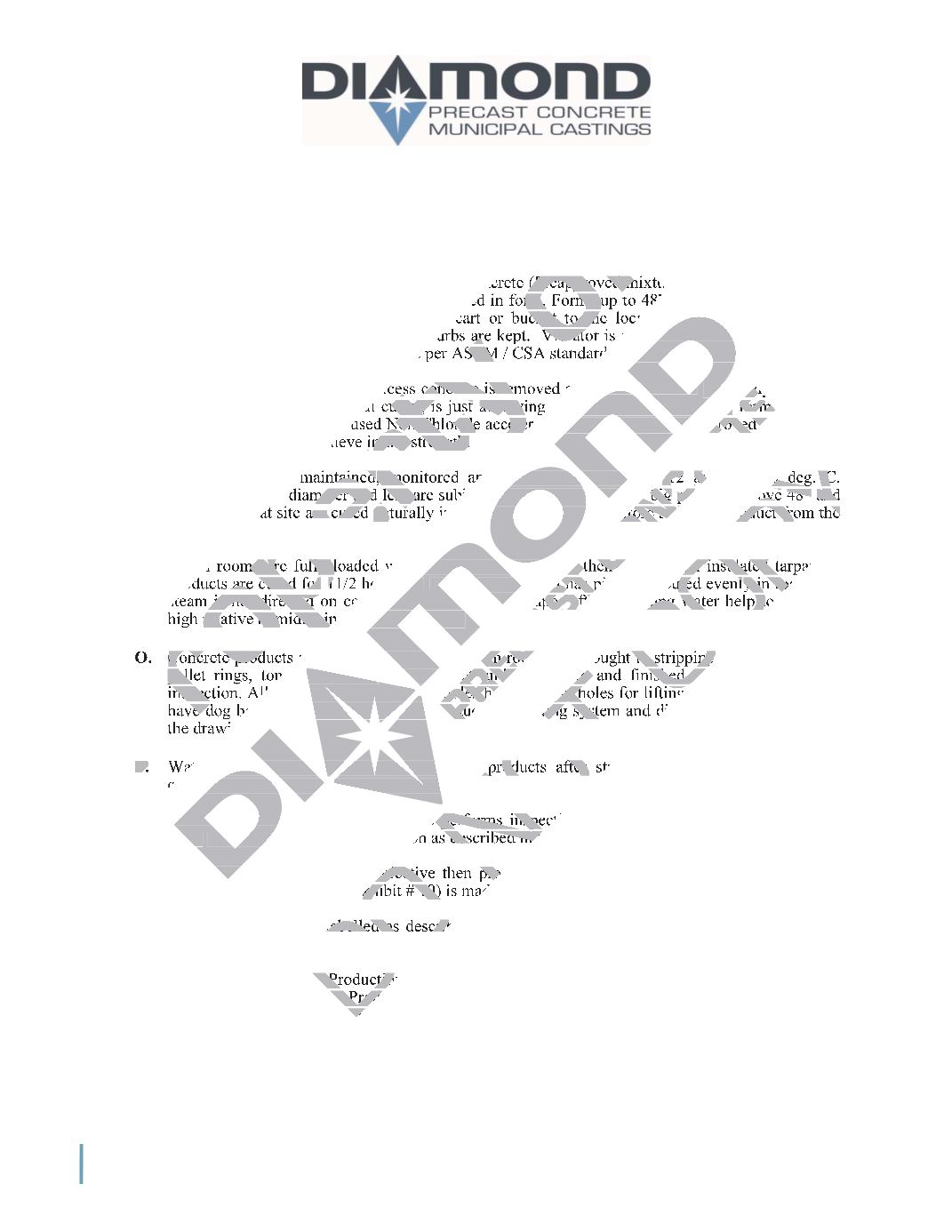
8
DIAMOND Precast Concrete Ltd.| 7520 Conrad St | Burnaby, BC V5A 2H7
Tel: 604.415.5181 | Fax: 604.415.5185 |
www.DiamondPrecast.comSection: 3
Date: 12/03/2015
Edition 1, Revision: 0
Page: 3 of 3
K.
Calibrated Volumetric Mixer produces the concrete (Preapproved mixture ratio of Cement, Sand,
Birdseye, water & NCA admixture) is poured in form. Forms up to 48” are brought to the mixer
and poured while concrete is taken in cart or bucket to the location where big forms, lids,
trenches, meter boxes, drain box and curbs are kept. Vibrator is used for duration of 30 seconds
at every foot of the pouring length as per ASTM / CSA standard to achieve required density.
L.
Concrete is levelled in form, excess concrete is removed and area is cleaned and ready for initial
curing in steam room. (Initial curing is just achieving sufficient strength to strip form and have
quick turnaround). We do used Non Chloride accelerator from Sikka which approved as per CSA
which helps them to achieve initial strength.
M.
Steam rooms are maintained, monitored and recorded in Exhibit # 12 at 60 to 70 deg. C.
Manholes of 48” diameter and less are subjected to initial curing. All big
products above
48”
and
other poured at site are cured naturally in forms for @ 24 hours before stripping product from the
form.
N.
Steam rooms are fully loaded with concrete products and then closed with insulated tarpaulin.
Products are cured for 11/2 hour to 2 hours. Steam room has pipe distributed evenly in room and
steam is not directed on concrete products. Steam vapor after becoming water help to maintain
high relative humidity in the concrete form.
O.
Concrete products are then removed from steam room and brought to stripping station to remove
pallet rings, tongue top ring, outer Jacket and inner core and finished product is ready for
inspection
. All products below 42” manholes have two pin holes for lifting while bigger products
have dog bone EZ lift pins to lift the product. The lifting system and direction is reflected on to
the drawings.
P.
Water is sprayed immediately on concrete products after stripping to maintain humidity in
concrete mostly required in summer time.
Q.
ACI certified Level II QC Inspectors performs inspection of finished product. He updates the
daily Progress Sheet of the inspection as described in Section 7.
R.
If finished product is found defective then procedure described in Section 11 is followed and
Non-Conformance report (Exhibit # 19) is made and hold tags are placed (Exhibit # 20)
S.
Finished Products are labelled as described in Exhibit # 21 and sent for storage as described in
Section 13.
T.
At the end of the day, Production Planning Sheet (Exhibit 17) filled by Production Supervisor
and Check list of Daily Production Batch (Exhibit # 12) filled by QC inspector in charge is
given to Production Manager to review and recorded and sign off.
U.
All the required documentation related production and QC are retained and stored in PM’s office.
PRECAST CONCRETE
Property of
DO NOT COPY