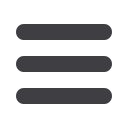
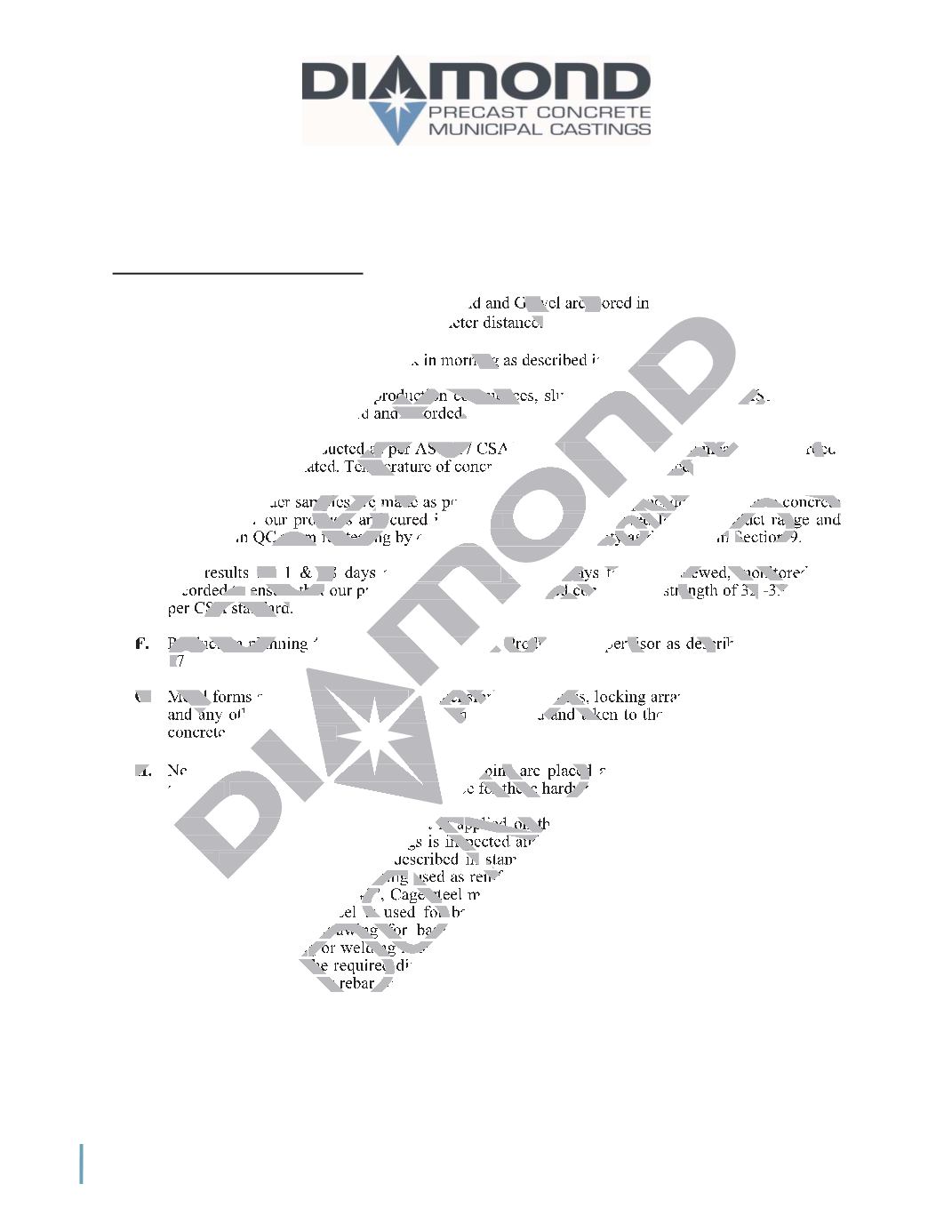
7
DIAMOND Precast Concrete Ltd.| 7520 Conrad St | Burnaby, BC V5A 2H7
Tel: 604.415.5181 | Fax: 604.415.5185 |
www.DiamondPrecast.comSection: 3
Date: 12/03/2015
Edition 1, Revision: 0
Page: 2 of 3
Actual Manufacturing Process
:
Diamond Plant is in enclosed building where Sand and Gravel are stored in controlled environment.
Cement is stored Silo and located at 50 meter distance.
A.
Concrete mixer is set once in a week in morning as described in QC Section 6.
B.
After Calibration and before production commences, slump tests done are as per ASTM / CSA
standard. Tests are measured and recorded.
C.
Air content test is conducted as per ASTM / CSA standard. Tests results are measured, recorded,
and density is calculated. Temperature of concrete is measured and recorded.
D.
Concrete cylinder samples are made as per ASTM / CSA standard procedure from same concrete
mix used for our products and cured in same procedure as followed for our product range and
then kept in QC room for testing by own developed testing facility as described in Section 9.
E.
Test results for 1 & 28 days and occasionally 3 & 7 days too are reviewed, monitored and
recorded to ensure that our product range achieves desired compressive strength of 32 -35 Mpa as
per CSA standard.
F.
Production planning for the day is given to the Production Supervisor as described in Exhibit #
17
G.
Metal forms are cleaned, inspected - dimensional, roundness, locking arrangements, joints, seams
and any other damages or repairs and then assembled and taken to the wet Mixer section at the
concrete pouring station.
H.
Necessary hardware’s like step pins, lifting pins are placed at proper lo
cation as described in
stamped
drawings. Certificate of compliance for these hardware’s are checked and documented.
I.
At Mixer, Bio gradable release agent is applied on the surface of forms. Steel supplied as per
specs specified in stamped drawings is inspected and approved is only used. Reinforced steel is
placed in form with spacers as described in stamped product drawing (Exhibit # 3). There are
three different kinds of steel being used as reinforcement material. Deformed steel hoop ring for
catch basin for size below 42”, Cage st
eel made from deformed steel is used for manholes sizes
above 36”
and rebar steel is used for bases and lids and covers. Most of the rebar steel is
prefabricated as per drawing for bases and lids. The spacers are well defined in stamped
drawings. No tackin
g or welding is done as our plant. Cage steel is received in rolls of 8’ x 300’
and is fabricated to the required dimension as per drawing and are tied by steel wire. Fabricated
steel either cage steel or rebar steel for bases are placed manually in the form free from mud, oil,
dirt & scale.
J.
The QC in charge continuously monitors and inspects the production progress sheet (Exhibit 12)
as described in Section 6
PRECAST CONCRETE
n
Property of
DO NOT COPY